Have a question about any of the products below? Need a quote or more information? Feel free to contact us using the menu above or the link at the bottom of this page.
Introduction
Sonochemistry is a field that uses high-power ultrasound — specifically cavitation — to promote and accelerate chemical reactions — with or without catalysts or additional reagents typically used in conventional chemistry.
Ultrasonic frequencies generally range from 12 kHz to several megahertz. However, cavitation does not have the same effect depending on whether low-frequency (F < 100 kHz) or high-frequency (F > 100 kHz) technology is used. Indeed, cavitation generated at low frequency primarily produces mechanical effects, while high-frequency cavitation mainly produces chemical effects.
Sonochemistry was first recognized as effective for heterogeneous reactions in the 1920s. By improving mass and heat transfer, ultrasound enabled better access of a reagent to a catalyst thanks to degassing and mixing induced by cavitation. It wasn’t until the 1950s–1970s that high-frequency technologies began to emerge, producing promising results for homogeneous reactions.
How does sonochemistry work?
Cavitation is created when ultrasonic vibrations are strong enough to vaporize a small amount of liquid, forming a vapor bubble.
This bubble then undergoes cycles of compression and expansion until it reaches a critical diameter, leading to its implosion:
These phases—expansion, compression, and implosion—are the site of numerous reactions either inside the bubble, at its interface, or in the surrounding liquid.
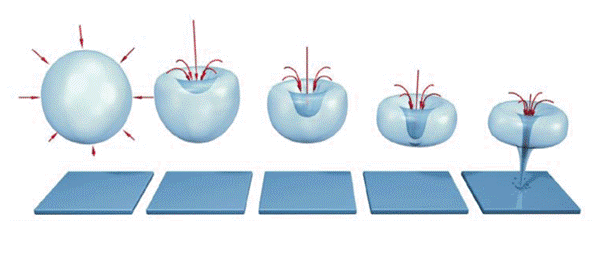
In the liquid medium, cavitation leads to the formation of hydroxyl radicals, which react with dissolved chemical species, mainly by oxidation.
Inside the bubble or at its interface, extreme temperatures (850 to 5200 °C) and pressures (1 to 1000 bar) trigger pyrolysis reactions.
Although these two phenomena occur simultaneously, their respective effects on a molecule depend on whether it is hydrophobic or hydrophilic. Generally speaking, hydrophobic molecules tend to undergo pyrolysis, while hydrophilic molecules are more affected by radical species in the solution. Surfactant molecules may be subjected to both processes.
Our Solutions for Sonochemistry
To generate acoustic cavitation, several components are required — at a minimum:
🔹 A linear amplifier to amplify an electrical signal to the desired amplitude;
🔹A function generator to transform an input signal into an electrical signal at the desired operating frequency;
🔹A ceramic or group of ceramics to convert the electrical signal into displacement amplitude (cavitation occurs once this amplitude is sufficient).
Limitations of Linear Amplifiers
Most current high-frequency technologies rely on radiofrequency linear amplifiers. These amplifiers do not include regulation strategies for frequency or power and therefore cannot adapt to the natural acoustic variations that occur over time.
As a result, the reproducibility and robustness of results obtained with these technologies remain critical and are not guaranteed.
Advantages of Our Ultrasonic Systems
🔹 SinapTec has developed a high-frequency equipment technology that ensures real-time tracking and regulation of both frequency and power.
🔹 This technology allows for repeatable and consistent results, whether your process is batch-based, in recirculation, or continuous.
🔹 It also ensures maximum ultrasonic treatment efficiency by consuming only the amount of energy necessary to achieve the desired result.
🔹 Under the same operating conditions, a technology with frequency control can achieve a 20% higher calorimetric efficiency compared to linear technology.
Our Sonochemistry Equipment
SinapTec offers a stable range of high-frequency ultrasonic equipment for laboratories.
These systems are used in various industrial and academic laboratories in France, Germany, China, and other countries to optimize tomorrow’s chemistry and develop alternatives to conventional chemical engineering processes.
They consist of:
🔹 An electronic generator that converts mains power into a sinusoidal electrical signal at the ceramic’s operating frequency;
🔹 A cup-horn that houses piezoelectric ceramics and converts the electrical signal into mechanical vibration;
🔹 A double-jacketed reactor placed on top of the cup-horn. This reactor maintains the reaction temperature if needed, and its dimensions can vary depending on your requirements.
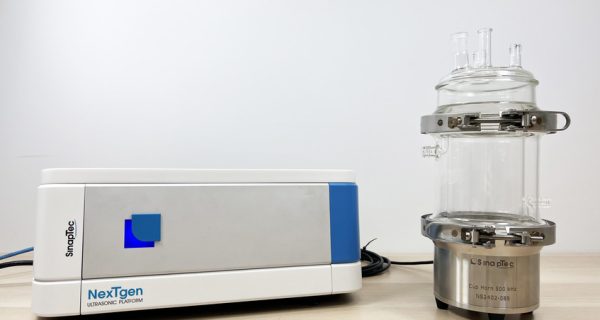
This setup can be equipped with various accessories such as a lid with input and output ports for temperature monitoring (with or without connection to the generator), inert gas purging, a mechanical stirrer, etc.
What about industrial applications?
This high-frequency technology can be manufactured and adapted to meet industrial needs.
For example, let us tell you about our involvement in the European PROMISCES project.
SinapTec contributed to this project by providing a technology to treat PFAS (per- and polyfluoroalkyl substances) from contaminated soil.
Our batch tests at laboratory scale successfully destroyed up to 97% of various long- and short-chain PFAS and reduced the toxicity of the ultrasound-treated solution. The final stage of the project led us to design a pilot-scale sonochemical reactor enabling recirculation treatment.
Beyond maintaining the performance mentioned above, this equipment also enabled a 60% reduction in energy consumption compared to lab-scale treatment.